Vacuum Casting and Color Customization: How to Get the Best Results
Vacuum casting is a popular method for producing plastic parts in small volumes. However, when it comes to color customization, vacuum casting presents some challenges. Adding pigments to the casting material can result in surface imperfections by parting lines and destroy the exterior cosmetic surface, and it is difficult to fix manually after the plastic parts are vacuum casted. Moreover, we have to manually remove burrs or improve the exterior cosmetic surface for the vacuum casted parts, which will also destroy the outlook and brings surface imperfections. In this blog post, we will explore a solution to this problem: spray painting the exterior surface of vacuum casted parts to achieve the desired color, while keeping the interior in its natural color.
- Step 1: Vacuum Casting in Natural Color
The first step in this process is to vacuum cast the part in its natural color, which is typically white or translucent. This is done to ensure that the interior of the part remains clean and free from any pigments that could affect its mechanical properties or performance. Vacuum casting in natural color also allows for easier quality control and inspection, as any defects or impurities will be more visible.
- Step 2: Surface Preparation
Once the part is vacuum casted, it’s time to prepare the exterior surface for painting. This involves cleaning the surface to remove any dust, oil, or other contaminants that could affect the adhesion of the paint. Sanding or polishing may also be necessary to smooth out any part lines or surface imperfections. It’s important to be careful during this step, as any damage to the exterior surface could compromise the overall quality of the part.
- Step 3: Spray Painting
With the surface properly prepared, it’s time to apply the paint. Spray painting is the preferred method for this application, as it provides an even coat of paint and allows for precise control over the color and finish. It’s important to choose a paint that is compatible with the casting material and can withstand any environmental or chemical exposure that the part may encounter in its end-use application.
- Step 4: Quality Control and Inspection
After the paint has dried, the part should be inspected for any defects or imperfections. This is an important step, as any flaws in the painted surface could detract from the overall quality and aesthetics of the part. It’s also a good idea to perform some basic tests on the part to ensure that the paint has not affected its mechanical properties or performance.
Just one catch that we want to highlight at the end:
The interior surface of the vacuum casted plastic parts is not suggested for color customization by spray painting. There are always jigs & fixtures to support the vacuum casted plastic part during the spray painting, there are contact points on the interior surface; moreover, there are always ribs & caves inside the vacuum casted plastic parts itself, which make it is a bit hard to get perfect color customization inside; In our factory, our customers always just leave it the natural colors, and please refer to below images for detail of the color customization on the exterior surface, as well as what the interior surface looked.
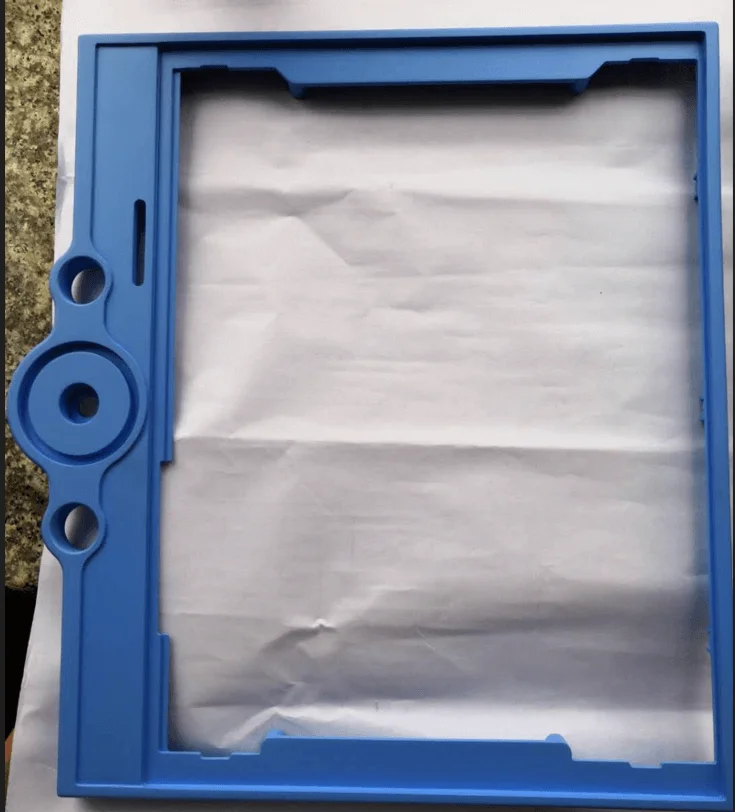
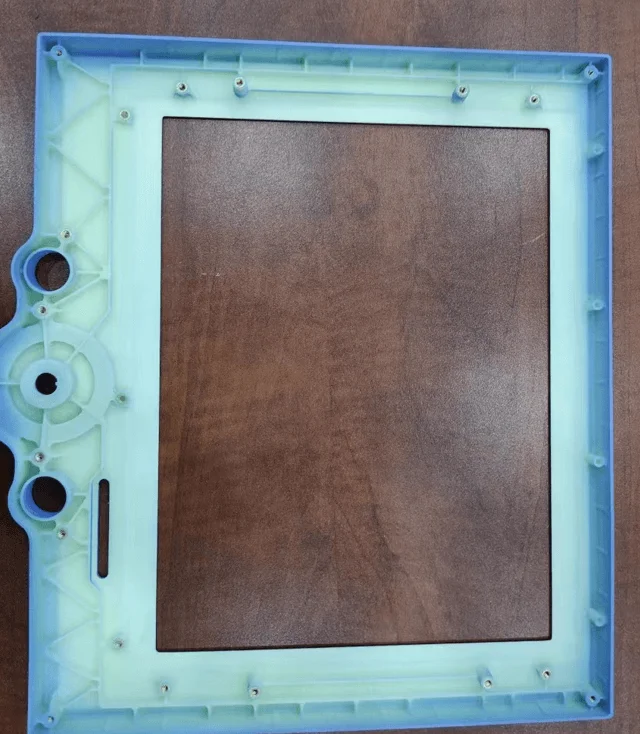
If you have any query regarding the color customization for vacuum casting, or need any vacuum casting service, please feel free to visit: Vacuum Casting from China | The Ideal Solution to Small Series Manufacturing in 2023! (vacuumcastingsz.com).
[…] options can also significantly impact the appearance and functionality of your polyurethane parts. Painting, machining, and coating are just a few examples of post-processing options that can help improve […]
https://karimmassimov.com/
karimmassimov.com e3a63d8